The production of ingredients that go into alcoholic beverages such as beer and whisky, along with the production of the drinks themselves are energy intensive. Whilst British distillers such as William Grants have been producing low carbon power using combined heat and power (CHP) for a number of years the opportunities for the whisky and brewery supply chain to do this has been less well explored. CHP for the distillery and brewery supply chains has applications both for malting operations and yeast manufacture. Typically this will involve the deployment of a gas engine fuelled either by pipeline natural gas, or alternatively biogas.
Malting Industry CHP
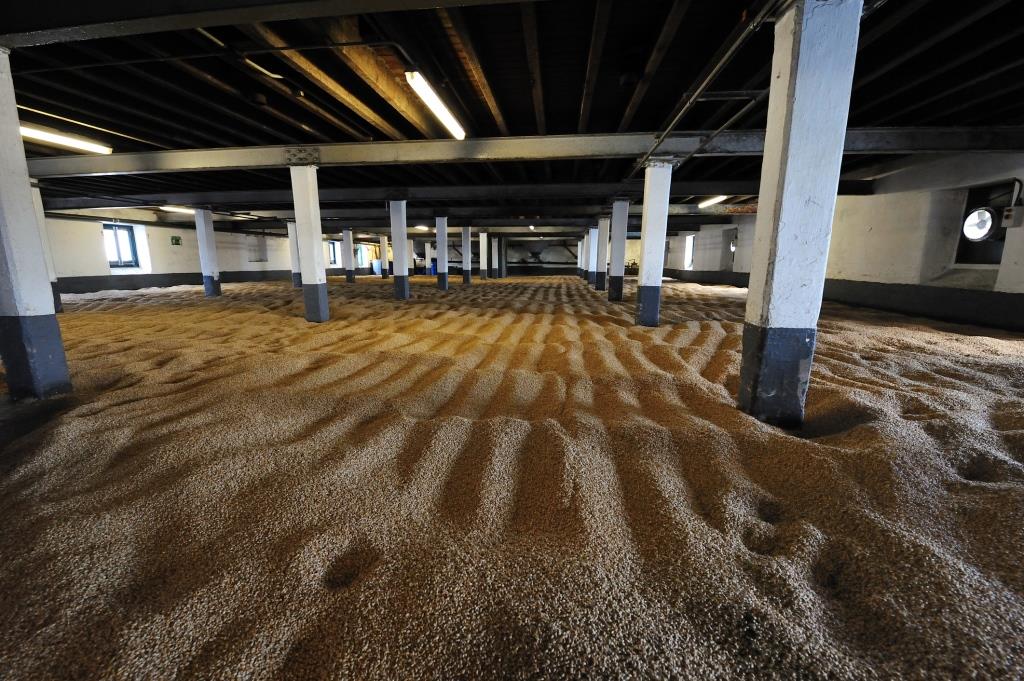
A malting room at a distillery (source: Istockphoto, Frankonline)
Malting is the process that converts grains into malt. Malt is primarily used in the production of beer (brewing) and whisky. It can also be used to make malt vinegar or malt extract. A traditional malting floor germinates the grains, which can be barley, sorghum, wheat or rye, in a thin layer on a solid floor. The floor can be manually raked or raked with automation which requires electricity. There is a requirement for heat both at the start of the process and end of the process. Initially barley received at the malt house with a moisture level over 13% must be dried in order for it to be safely stored.
The germination process of the grain that commences prior to the production of the ma
lt produces heat. The raking and aeration helps to maintain a constant temperature. Kilning – the process that reduces the moisture content of the grain and stops germination at the correct stage occurs through the addition of further heat. The temperature reaches in excess of 80˚C in the final stages of the process.
Yeast Industry CHP
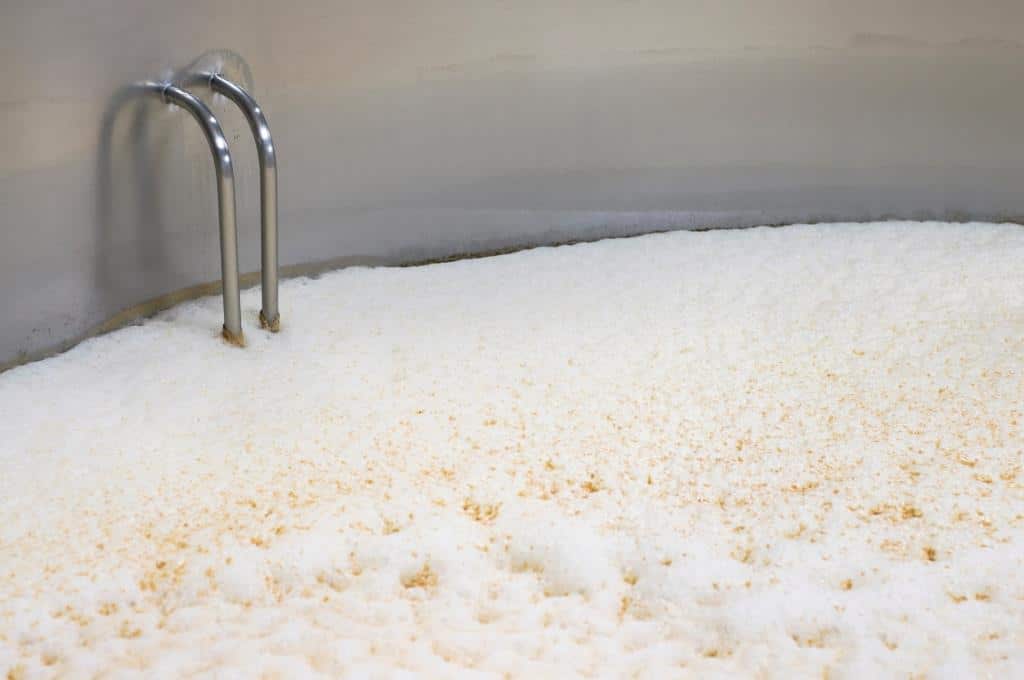
Beer brewing in action using yeast (source: Istockphoto: George Clerk)
Yeast is key to the production of beer and whisky. In beer production yeast feeds upon sugars which are used as an energy source. Alcohol is produced as a by-product of this process. In industrial yeast production there are a number of elements that require heat. These include sterilisation, using steam and heating of the process to the optimal temperature for the reproduction of the yeast cells. Also in the event a dried yeast culture is required, further heat will be needed to evaporate excess water,
The increased automation of industrial malting and yeast production facilities means increased electrical demand. The heat requirements of drying, production, storage and kilning of the final product, means these plants can benefit from the deployment of combined heat and power (CHP) technology. These systems can use gas engines operating either on pipeline natural gas or alternatively biogas which is a renewable fuel.
When the gas is used as a fuel in the gas engine, both electricity and heat are produced, both of which can be used for local energy needs. This is a win-win as not only does it reduce costs, carbon emissions can also be reduced or negated.
As a company Clarke Energy has supplied almost 300MW of natural gas fuelled CHP plants in the UK alone. CHP for the distillery and brewery supply chains offers potential for cost and carbon savings.