Dairy Industry CHP / Cogeneration
Combined heat and power (CHP) or cogeneration has significant potential in the dairy industry. Electricity and heat recovered from a gas engine captive power plant can be deployed for useful onsite us. Converting the heat into cooling via absorption chillers is called combined cooling heat and power or trigeneration, and can be deployed to support the dairy’s cooling requirements.
Benefits of CHP for dairies
- Energy costs savings – Overall efficiency (electrical and thermal) can reach 95 percent using a wide fuel range
- Resilient and robust power – You don’t have to rely on the grid alone to ensure your facility has the power it needs 24/7
- Environmentally friendlier – Less fuel burned per MW generated at lower CO2 emissions. DLE technology can sustain lower emission levels while eliminating system water requirements
- Standardized design – Smaller footprint, sizable to your unique spatial requirements
- Flexible power – Thermal energy can be stored for use, electricity can be fed into the public grid or used for artificial lighting, and an optional full island lighting control system is available
CHP in the dairy industry
Milk production takes place in numerous countries across the world and is of great importance to the agricultural sector, representing a significant portion of its value.
The European annual milk production is estimated around 152 million tonnes. The main producers in the European Union are Germany, France, the United Kingdom, the Netherlands, Italy and Poland. Together, they account for a rough 70% of the EU production. According to the EU Milk Market Observatory, a trending product with two digit growth rates is milk powder. The European Commission expects further growth in the European dairy sector despite some downward price issues in the current market. The growth is driven by the steadily increasing world demand and a continuously high domestic consumption.
Factor | Unit | Value |
Milk energy consumption | kWh/l | 0.1-0.2 |
Milk water required | l/l | 0.6-1.8 |
Milk waste water | l/l | 0.8-1.7 |
Powdered milk energy consumption | kWh/l | 0.3-0.4 |
Powdered milk water required | l/l | 0.8-1.7 |
Powdered milk waste water | l/l | 0.8-1.5 |
Raw milk is a versatile commodity. In a dairy, in can be converted into various products – milk and cheese production reach highest annual global production volumes. Common to each product are the initial processing steps, namely clarification and pasteurization, already consuming large amounts of energy to reach temperatures around 95°C. The subsequent processing varies with the desired product. Energy intensive manufacturing steps are spray drying the powdered milk and condensation for condensed milk. Also, the bottling of milk requires energy in the form of heat to disinfect the bottles delivered. Throughout the production chain, raw milk and products must be stored at chilled temperatures, requiring energy in the form of refrigeration to maintain the quality of the processed goods. Since many nowadays dairies are multi-product facilities, an elaborated energy concept is of steadily gaining importance.
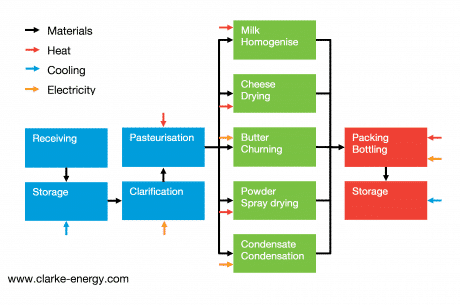
A flow chart highlighting typical processes in the dairy industry and potential heat, cooling and electricity loads for CHP and trigeneration applications.
CHP potential in dairies
The share of the energy costs in the gross added value in dairies vary significantly with the products with a spread of factor 10 in specific energy demand of different products. Thermal energy is required for flash boilers for pasteurization, bottle washing, drying, condensing, air condition and cooling. With the rise of automation technology, automated packing and filling, electric energy is gaining an increasing share in the overall energy costs.
Three main aspects positively affect to efficiency of the dairy process and increase the potential for CHP integration:
- Increasing the number of low temperature processes
- Use waste energy from CHP plants in absorption chiller to provide cooling
- Increase the steadiness of your consumption
In many dairies, heat consuming processes are provided with steam, which is not necessarily required, but can also take place by using low temperature heat at around 95°C. These low temperature requiring processes bear significant potential to run on waste heat from CHP systems. As such, the heat recovering systems can be optimized for maximum efficiency while simultaneously increasing the power output from the CHP plant.
In addition to providing low temperature heat to the production process, refrigeration can also be achieved by CHP systems. Many dairies require cooling for iced water or cooled storage. Most often, cooling is provided by air cooling utilities that run on electricity – causing high operational costs. Since dairies usually run 24/7, the demand for cooling is high and steady – perfect conditions for CHP. Heat from sources such as the exhaust gas can be used in a trigeneration arrangement to generate cooling from waste heat. As such, you are not only avoiding electricity to run your refrigerating facilities – you also provide efficiently generated electric energy to the grid.
Additionally, the steadiness in consumption of energy allows for continuous and planned operation of a CHP facility resulting in decreasing costs and optimal availability management of your plant. You can also run a CHP plant on biogas produced in digesters and fermenters from biogenic waste of the production process.
To learn more about data center CHP or for us to evaluate your project please submit your enquiry here.