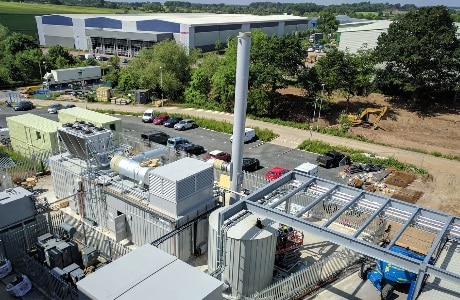
The Plastic Omnium, Base Power, combined cooling heat and power plant (CCHP) supplied by Clarke Energy
Plastic Omnium Automotive Ltd (POA) is a world leader in the design and manufacture of external automotive body parts. The division serves 15% of the global market for leading car manufacturers including Jaguar Land Rover and Nissan.
The company’s operations are heat and power intensive. POA’s site at Measham, Derbyshire, required a solution to dramatically lower costs, emissions and support a more resilient infrastructure. A solution using combined cooling, heat and power (CCHP) or trigeneration via gas engine technology was able to achieve this.
POA employed BasePower to develop and install an onsite CCHP solution within a 12 month timeframe. The scheme is set to reduce energy usage and peak summer cooling demand, whilst saving over 500 tonnes of CO2 emissions per annum.
The electricity generated provides power for the manufacture of injection moulded automotive exteriors. Heat produced from the CCHP is utilised throughout the factory’s critical areas, including paint shops and cooling to moulding equipment.
As heat demand decreases over the summer months, CCHP begins. Surplus heat generated is utilised through an absorption chiller, offsetting site cooling loads. The CCHP scheme ensures that limited heat is wasted.
Energy costs will be dramatically reduced due to a lower electrical load being imported from the grid.
BasePower contracted Clarke Energy to engineer and install one of GE’s Jenbacher JMS612 reciprocating gas engines for the trigeneration plant, producing an electrical output of 2MW at 44% efficiency.
Clarke Energy evaluated site demand and delivered a package that:
- Interfaces to the existing site
- Utilises electrical thermal energy, ensuring the most commercially viable returns
- Improves system reliability and site resilience.
The energy centre is packaged off-site in a weatherproof, acoustically lined steel container, complete with a forced draught ventilation system providing the required cooling and combustion air for the generator set.
Installation was coordinated with system shutdowns to ensure no impact to the factory’s production. Commissioning and G59 grid electricity grid synchronisation took place in June 2017, keeping within a strict construction and commissioning time frame.