Power distribution networks across Africa are notoriously unreliable. Frequent power interruptions can be enormously costly for many of the continent’s factories. Not only do power outages disrupt production batches, they can also damage or reduce the life of important plant components such as kilns. This too has a knock-on effect on wider the country’s gross domestic product – less power at higher costs means reduced output and less business revenue within the state. Captive power plant efficiency is an important dynamic in improving competitiveness and generating cost effective, low carbon power.
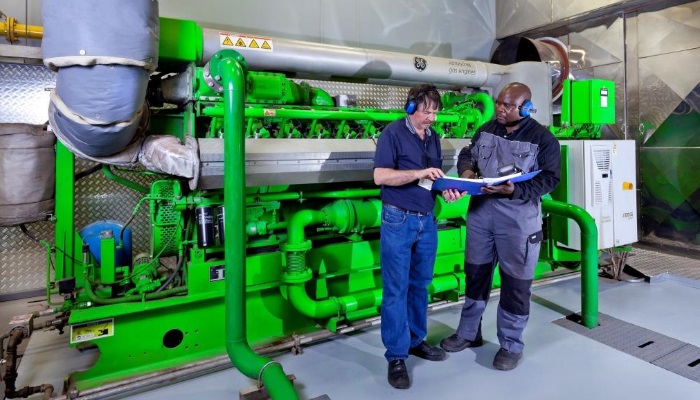
MTN’s cogeneration plant in South Africa
Self-generation of power is hugely popular for industrial facilities across Africa. Self-generation with genset-based captive power plants provides business operators control and understanding about their own power supplies. There is a convergence with other businesses on the international stage. Many developed countries are moving away from large centralised power plants, and towards a more localised efficient power generation network. It’s important therefore for African businesses to follow this lead, and when selecting power generation equipment to focus on, cost reduction, fuel efficiency and reliability to compete on the international stage.
There are scores of inefficient generators on the African continent that either have high fuel consumption of that do not maximise the potential of the energy in the fuel.
Gas is set to become the most important fuel for power generation over the next 30 years. The availability across sub-Saharan Africa is limited, either by the fuel distribution network, or by the physical availability of gas in the pipelines. Nigeria has the most developed gas distribution network in sub-Saharan Africa. Following the first natural gas fuelled captive power plant in Nigeria in 2002 that was developed by Clarke Energy at a now closed Dunlop Tyre plant, the technology is fuel of choice for industry in southern Nigeria with a number of hundred MW of installed capacity in the region.
Nonetheless there is significant opportunity to further increase fuel efficiency through the addition of heat recovery systems – or combined heat and power technology. Here the heat from the generator is recovered as hot water or steam for localised use. If there is insufficient demand for the heat, the technology can be taken a stage further with the use of absorption chillers – a process called ‘trigeneration’ or combined cooling heat and power. Diageo’s Guinness Ogba brewery lead the way here at their captive power plant that not only generates reliable supplies of electricity, but also hot water and cooling to aid the brewery’s operation.
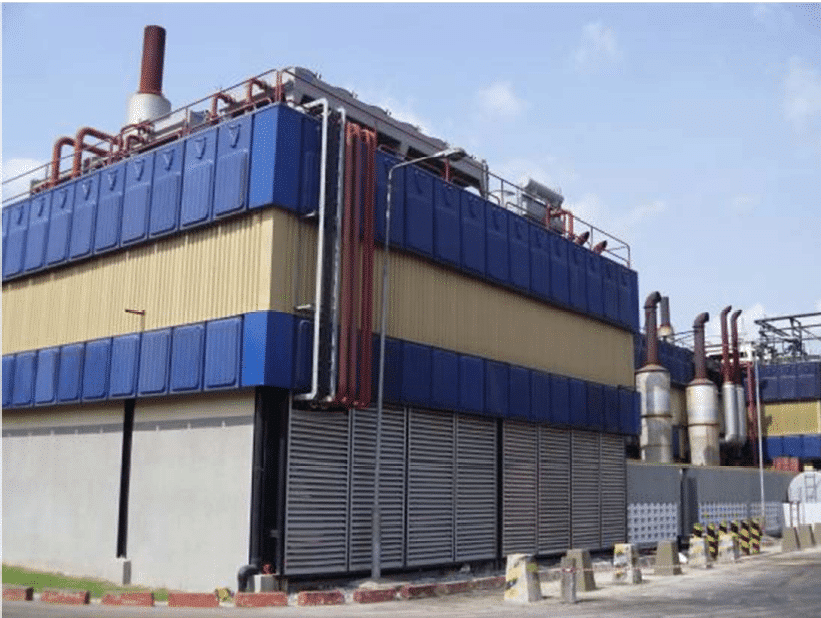
Guinness Ogba’s trigeneration facility in Lagos, Nigeria
Where there is no access to pipeline natural gas, there is still the potential to use this valuable fuel, if it is compressed as compressed natural gas (CNG) loaded on to trucks tha act as transportation and gas storage on the site of use. Nestlé’s Flowergate factory near Lagos in Nigeria pioneered this approach in West Africa. It has since been expanded to numerous other sites including the University of Port Harcourt.
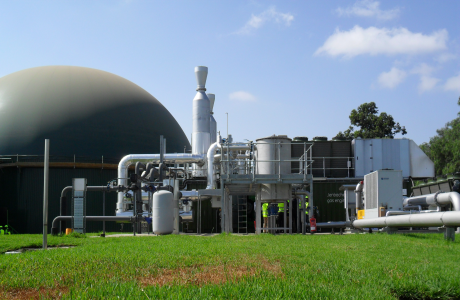
Tropical Power’s biogas plant at Gorge Farm near Lake Naivasha in Kenya
Another concept for power generation is the production of biogas from waste produced in the locality of the power user. This technology has potential at breweries, food processing plants or commercial farms. Waste such as plant material or food trimmings can be macerated and input into anaerobic digesters that harness naturally occurring microbes to create biogas, a renewable fuel. This gas is then utilised in a biogas engine for reliable onsite power. Tropical Power have developed the largest grid connected biogas plant in Africa at a site near Lake Naivasha in Kenya. The owners flower farm has significant local demand for energy. Tropical Power developed the system to recover wastes from the immediate and surrounding farms to generate 2.6MW of renewable power. During times when they do not need all the power they are able to sell the energy to the national grid, helping improve local power supplies significantly and boost local power generation. The heat is also utilised for heating a nearby greenhouse – making the best use of the valuable renewable fuel.
If diesel is the only local option for power generation as a fuel, then it is important to maximise the power generation from it. GE has recently developed a new high efficiency ‘616’ 2.5MW diesel engine, based around its highly efficient gas engine technology. This has a low fuel consumption of 184g/kWh, compared to many less efficient units of around 210g/kWh. This difference translates to around $200,000 per year at $1per litre fuel cost, not to mention reduced carbon emissions. This technology has been installed at Flour Mills of Nigeria’s operations in Lagos, who were another early adopter of gas engine technology.
In summary captive, embedded power is driving industry in the African continent. Maximising energy efficiency with combined heat, power and cooling technology is in important dynamic in reducing costs and carbon emissions. Innovative thinking and technologies are playing a key role in many new African markets.